In a discussion about any irrigation system, it is common to hear terms such as pump curve, system curve, and Variable Frequency Drive (VFD). It is essential to understand what these terms mean, how they all work together, and how to use that information. Being able to read a pump curve, whether it is a fixed speed or variable speed pump, can help you achieve long-term savings in energy costs, minimal irrigation system repairs, and avoid catastrophic failure (explosion emoji).
Fixed speed pumps are simple to read. There will be several lines on individual scales in modern fixed-speed centrifugal pump curves (Figure 1). The pump performance curve, efficiency curve, power curve, and Net Positive Suction Head required (NPSHr) curve are included. Although each of these curves is vital to understand, the big focus is typically on the pump performance curve, representing the range of pressures that the pump can operate at the respectful range of flow rates. In Figure 1, the solid blue line in the top section of the graph represents the allowable operating region for that specific pump.
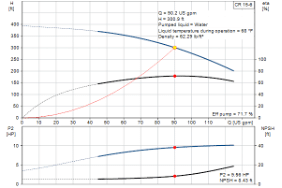
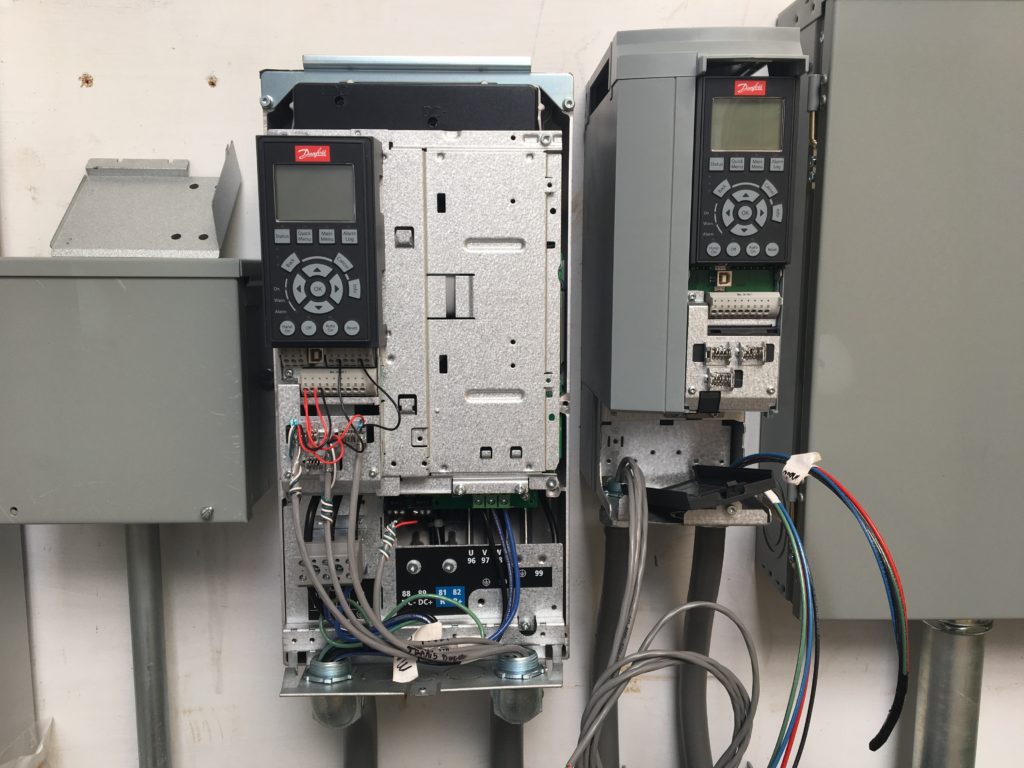
Operating the pump to the right of the curve (above 125 GPM) and the left of the curve (below 45 GPM) can result in premature failure of the pump. The solid black line below the pump performance curve represents the efficiency curve. In this case, the highest efficiency will be achieved when the pump is operating at approximately 90 pm and 300 feet of head. It is best to select a pump that is as close to the highest efficiency point as possible to allow variations in flow without damaging the pump or the irrigation system.
In an irrigation system, the system curve represents the amount of friction loss present with a specific flow rate from the pump discharge to the outlet of the emission device (drip tape emitter, sprinkler, etc.) with virtually zero pressure. Any change in flow, whether it is an increase or decrease, will result in a change in friction loss. When calculated correctly, the intersection of the system curve with the specific pump curve will represent the actual performance of that particular pump in that specific system. The red line in Figure 1 illustrates the system curve that will result in the highest pump efficiency: approximately 70% at 90 pm 300 feet of head.
When a VFD is installed, an entirely new range of pressure and flow rates is used for the pump. The darker blue shaded region represents the preferred operating region for a pump driven by a VFD in Figure 2. The VFD allows the speed of the pump to vary, which results in multiple operating pressures at the same flow, and vice versa. In the image, the red curve represents the system curve. The duty point (yellow dot) is set to 30 GPM at 100 feet of head. To achieve that point, the VFD will reduce the speed of the pump to 92% (blue line).
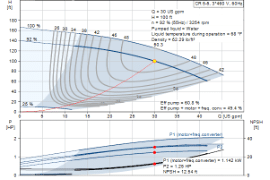
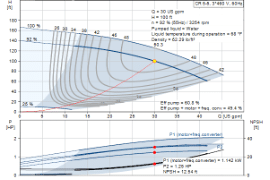
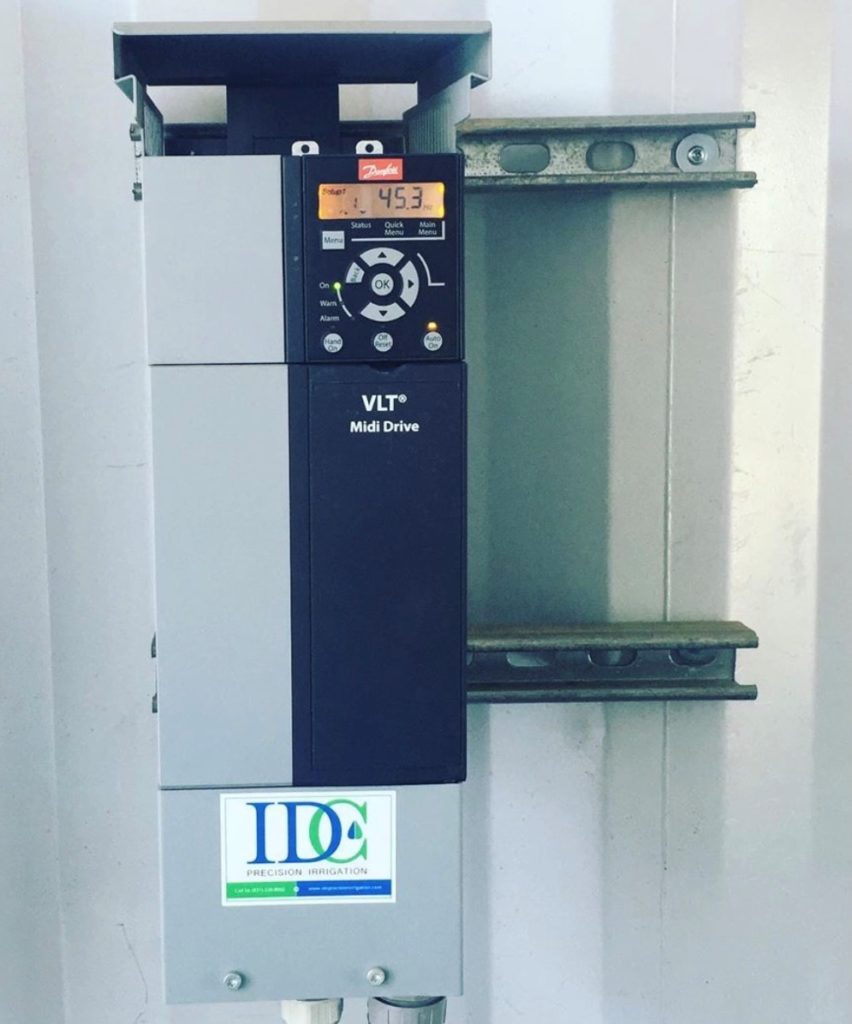
There are some misconceptions about what a VFD does for a system. It is common to see a constant-pressure system in agriculture which means that the drive is programmed to ramp the speed of the pump up and down to maintain a constant pressure at the pump discharge. A big selling point for this is that the VFD will “always drive the pump to operate at its highest efficiency.” This is false for a constant-pressure system. In Figure 3, the dark grey lines represent constant-efficiency curves, and the neon green line represents a constant pressure of 100 feet of head. If the operating pressure remains at 100 feet and the flow decreases (to the left of the yellow marker), you can see that pump efficiency decreases as it crosses the grey efficiency curves.
Pump and VFD selection is critical and takes a bit of research. Skipping steps to this can lead to unnecessarily high energy costs, endless repairs, and hair-pulling troubleshooting. If you have questions or need help specifying or trouble shooting a pump issue, feel free to reach out to me.
One Response
Great article Saul! Very useful information.